高強度鋼板代替?zhèn)鹘y(tǒng)鋼板可以減少車身重量,并提高碰撞安全性,實現(xiàn)汽車輕量化。 與傳統(tǒng)鋼板不同,高強度鋼板的成形需要內(nèi)部帶有隨形冷卻水道的熱沖壓模具,來保證零件的成形性要求以及良好的力學(xué)性能。
隨形冷卻水道的走向與模具型面的形狀基本一致, 且中心距離型面的距離都相同。內(nèi)部隨形冷卻水道的成功成形,是熱沖壓模具制造的重點及難點。 目前熱沖壓模具制造工藝中,鉆孔工藝可以加工方向不變的直水道,但是很難滿足隨形要求;鑲 拼工藝對密封提出很高的要求;鑄 造工藝中預(yù)埋不銹鋼管可以得到隨形的冷卻水道,但是冷卻效果不佳,而 預(yù)埋陶瓷芯存在去除工藝繁瑣等缺點。3D 打印技術(shù)是近幾年非常熱門的技術(shù),但是受制于打印材料的高成本,此項技術(shù)在工業(yè)生產(chǎn)上并沒有大面積應(yīng)用。
使用 3D 打印技術(shù)打印出普通造型方法難以成形的砂型(芯),對于結(jié)構(gòu)復(fù)雜的金屬零件, 特別是熱沖壓模具這種具有復(fù)雜內(nèi)腔結(jié)構(gòu)的金屬零件具有重要意義。
1 、技術(shù)路線
以某一款轎車熱沖壓模具為研究載體, 該熱沖壓模具的設(shè)計綜合考慮計算機 CAD 參數(shù)化建模、熱沖壓及淬火仿真分析、 水冷模具管道設(shè)計及優(yōu)化等科學(xué)問題。圖 1 為一個典型車身模具鑲塊, 該模具具有復(fù)雜型面, 由于隨形冷卻水道要跟型面走向一致且要跟型面距離相等,所以冷卻水道的結(jié)構(gòu)也比較復(fù)雜。
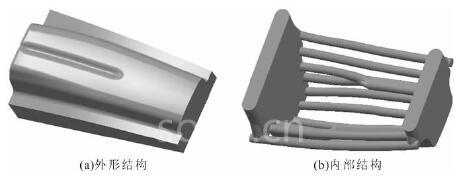
圖 1 鑄件的外形結(jié)構(gòu)以及內(nèi)部結(jié)構(gòu)
傳統(tǒng)鑄造工藝中, 冷卻水道部分需要通過下芯的工藝實現(xiàn),按照設(shè)計要求,每一根水道的形狀結(jié)構(gòu)不盡相同, 所以每一根水道的成形都需要設(shè)計相對應(yīng)的芯盒來實現(xiàn),工藝比較繁瑣復(fù)雜。 由于砂芯比較細,單根砂芯很容易發(fā)生偏移而造成最后成形的水道與設(shè)計出現(xiàn)偏差。在汽車熱沖壓模具的數(shù)字化鑄造工藝路線中,首先對模具鑲塊進行鑄造方案設(shè)計, 此部分包括鑄件分析、澆冒口設(shè)計以及分型設(shè)計;將得到分型各部分進行切片處理得到打印數(shù)據(jù),將打印數(shù)據(jù)傳輸?shù)?D 打印設(shè)備中進行加工制作得到相應(yīng)的砂型(芯);對砂型(芯)進行鑄造前處理,將各部分按照分型設(shè)計組合后進行澆注試驗;其中在各個加工制造過程中,使用三維掃描儀對各部分得到的產(chǎn)品,包括砂型(芯)以及最后得到的鑄坯進行掃描,然后進行精度評價。 圖 2 為整個工藝流程圖。

圖 2 數(shù)字化鑄造工藝路線
2 、鑄造方案設(shè)計優(yōu)化
2.1 鑄件分析
由于后期鑄造表面質(zhì)量并不能達到模具工作要求,模具型面需要后期機加工,而通過 3D 打印的砂型澆注得到的鑄坯精度很高, 僅需要一次精加工,加工余量不需要很大,取為 3 mm.
本試驗?zāi)康氖堑玫揭惶灼嚐釠_壓模具的數(shù)字化鑄造工藝路線, 主要為驗證基于此路線的模具及其冷卻水道的最后成形, 用鑄造高溫性能與模具鋼相似的 35 鋼代替驗證其成形性 ,鑄造縮尺為2.5%。
2.2 澆道與冒口的設(shè)計及優(yōu)化
由于模具的復(fù)雜型面一側(cè)為將來沖壓的工作面,所以這個工作面需要有比較好的鑄造性能,在鑄造方案設(shè)計時,將這個面置于底側(cè)。 采用底注式澆注方案,澆口設(shè)計在鑄件的最底端。
由于隨形冷卻水道的直徑大約在 10~12 mm,對應(yīng)的砂芯直徑也很細,鋼液澆注時, 需要保證鋼液在上升充型的時候要平穩(wěn),故采用 開放式澆 注系統(tǒng),減少鋼液對砂芯的沖擊。
澆道橫截面的面積比取∑F直∶∑F 橫∶∑F 內(nèi)=1∶1.2∶1.5,直澆道為阻流面,根據(jù)以下公式計算阻流面面積以及澆注時間:

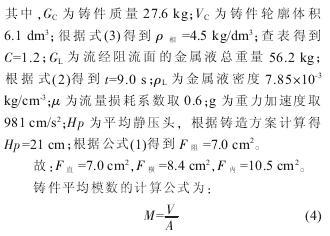
式中 ,V 為鑄件體積 3 540.05 cm3,A為傳熱表面積 1781.22cm2,根據(jù)式(4)可得,鑄件模數(shù) M=1.98cm。根據(jù)鑄件模數(shù),通過查,選取冒口為標(biāo)準(zhǔn)圓柱形冒口,其中直徑高度均為 120 mm。
依據(jù)計算得到的澆注系統(tǒng)以及冒口尺寸,鑄造方案設(shè)計如圖 3。 將設(shè)計的鑄造方案 CAD 數(shù)據(jù)轉(zhuǎn)化為有限元網(wǎng)格數(shù)據(jù)文件后,用 procast 鑄造模擬軟件對鑄造方案進行計算
,對澆注系統(tǒng)以及冒口的設(shè)計進行校核。
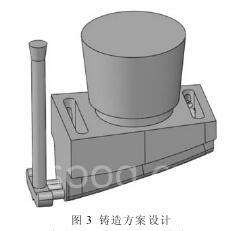
計算結(jié)果最后凝固位置位于冒口內(nèi),證明了冒口設(shè)置的合理性, 但是由于各部分砂型采用 3D 打印的方案制作,所以冒口的設(shè)計并不需要完全按照標(biāo)準(zhǔn)形狀設(shè)計,而可以參照模具的結(jié)構(gòu)進行單獨設(shè)計。 由于此模具呈長條狀,且一側(cè)質(zhì)量大于另一側(cè),所以設(shè)計冒口形狀為腰圓形,且腰圓形兩側(cè)圓弧并不相等,圓弧半徑較大的一側(cè)對應(yīng)于模具鑄件質(zhì)量比較大的一側(cè)。
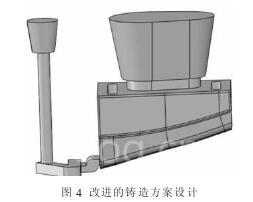
圖 4 中所示,改進的鑄造方案中冒口為腰圓形冒口。由于隨形水道的直徑比較小,對應(yīng)的水道芯的直徑也會比較小,為了降低澆注時鋼液對砂芯的沖擊,所以要考慮降低鋼液進入鑄型時的速度。 除了采用全開放的澆注系統(tǒng)外,在內(nèi)澆道與橫澆道上做一定的緩流設(shè)計,而由于采用 3D 打印制作的工藝,并不會因為澆道設(shè)計的復(fù)雜而增加制造難度。 圖 4所示,改進的鑄造方案設(shè)計中內(nèi)澆道與橫澆上有緩流設(shè)計。
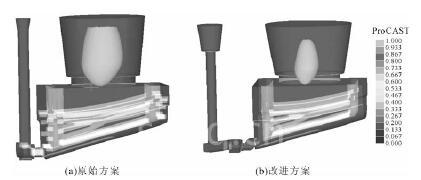
圖 5 最后凝固位置
腰圓形冒口形狀的設(shè)計, 可以起到標(biāo)準(zhǔn)圓形冒口相應(yīng)的補縮作用, 圖 5 所示為兩種冒口設(shè)計中計算的最后凝固位置, 以看到最后凝固位置都位于冒口中。由于腰圓形冒口與模具形狀相對應(yīng),可以減少冒口質(zhì)量從而提高工藝出品率。通過比較計算結(jié)果中鋼液流經(jīng)內(nèi)澆道時的速度, 可以發(fā)現(xiàn)在內(nèi)澆道橫澆道上做緩流設(shè)計可以減少鋼液進入鑄件的速度。

圖 6 鋼水流經(jīng)內(nèi)澆道的速度
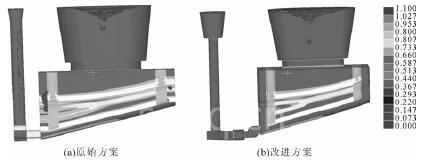
圖 7 縮松縮孔示意圖
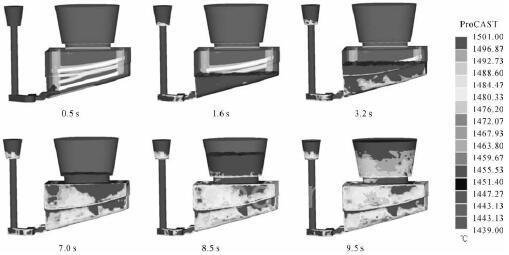
圖 8 充型示意圖
圖 6 所示為不同設(shè)計的澆道計算得到的鋼液流經(jīng)內(nèi)澆道的速度。比較兩種設(shè)計計算得到縮松縮, 可以發(fā)現(xiàn)改進后的方案鑄件內(nèi)部縮孔縮松明顯少于初始方案設(shè)計。 圖 7 所示為縮松縮孔計算結(jié)果。選定改進后的鑄造方案為實驗澆注方案, 圖 8所示為不同時間下的充型圖, 充型期間比較平穩(wěn)。3 3D 打印鑄型在完成鑄造方案的設(shè)計以及校核優(yōu)化后, 需要對鑄件的陰模進行分型設(shè)計。由于各個部分采用 3D打印工藝進行制作, 所以分型時并不需要像傳統(tǒng)砂型鑄造分型需要考慮的拔模問題。 考慮到最后各個砂型的組合以及 3D 打印設(shè)備制作效率, 將鑄件陰模分成四個部分:下型部分,砂芯部分,冒口部分,澆注系統(tǒng)部分。 圖 9 為鑄件陰模的分型設(shè)計。

圖 9 鑄件陰模的分型設(shè)計
采用 SLS 法(選擇性激光燒結(jié)法)加工打印各個部分。 由于砂芯部分中隨形冷卻水道芯比較細,打印砂芯不能使用一般的覆膜砂,因此采用強度指標(biāo)比較高的寶珠砂,可以保證打印成功率以及打印得到砂芯強度。 其他部分采用一般砂型所需要的普通覆膜砂。 打印過程中,調(diào)整打印設(shè)備中激光的掃描功率,以及打印設(shè)備腔體內(nèi)環(huán)境溫度,特別對于砂芯部分,由于結(jié)構(gòu)比較復(fù)雜,在加工時需要對打印參數(shù)精確控制。
各部分的加工參數(shù)見表 1。將 3D 打印的預(yù)成型產(chǎn)品放入烘箱中烘烤以使其強度滿足澆注要求。 為了防止在烘烤時發(fā)生變形,將砂型周圍埋上細小的玻璃珠。 表 2 為烘烤參數(shù)。

圖 10 所示為 3D 打印設(shè)備打印制作以及烘烤完成的砂芯以及砂型。打印制作的砂型的尺寸精度直接影響最后得到的鑄件尺寸精度。 使用三維掃描儀對打印得到的各部分砂型進行掃描測量, 將測量所得的點云數(shù)據(jù)與三維 CAD 數(shù)據(jù)進行精度比對, 確定砂型的制作誤差。 圖 11 為砂芯的精度比對結(jié)果,可以看出砂芯的整體制作誤差在 1.5 mm 以內(nèi),根據(jù)誤差分布圖以及誤差云圖顯示結(jié)果, 隨形水道部分對應(yīng)的砂芯制作誤差在0.75 mm 以內(nèi) , 且大部分誤差在0 . 30 mm 以內(nèi)。 由于砂芯部分對應(yīng)鑄件的隨形水道部分, 而最后隨形水道位于鑄件內(nèi)部無法測量其尺寸精度, 所以此時測量的砂芯精度可以為最后鑄件內(nèi)部的隨形水道尺寸精度提供參考。
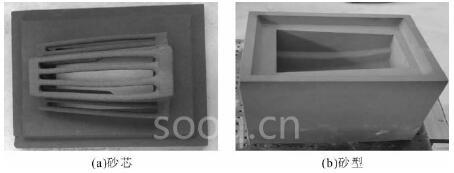
圖 10 砂芯與砂型

圖 11 砂芯精度檢測結(jié)果
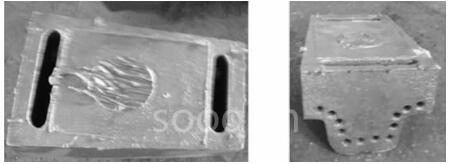
圖12 模具鑄坯
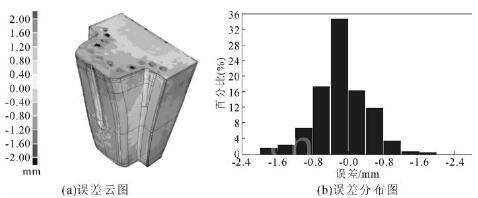
圖 13 鑄坯精度檢測結(jié)果
4 、澆注及澆注結(jié)果
將各部分砂型按照圖 9 的分型設(shè)計進行組合,組合完成后進行澆注,按照之前模擬計算得到的 1 560 ℃的澆注溫度進行澆注。 圖 12 為澆注得到的模具鑄坯, 使用三維掃描儀對鑄坯進行掃描后再進行精度評價。 圖 13 所示為鑄坯精度評價,根據(jù)結(jié)果發(fā)現(xiàn)鑄坯的整體尺寸誤差大部分集中在 2 mm 以內(nèi),工作型面的制作誤差在 1.2 mm 以內(nèi),根據(jù)誤差分布圖分析,大部分誤差在 0.8 mm 以內(nèi)。將模具進行剖分操作, 一方面檢驗其內(nèi)部水道的成形情況, 另一方面檢測模具內(nèi)部是否有縮松縮孔等鑄造缺陷。
圖 14 為鑄坯剖分結(jié)果,根據(jù)剖分結(jié)果可以看出,內(nèi)部冷卻水道完全成形,并沒有水道堵塞的情況出現(xiàn), 且模具內(nèi)部不存在鑄造缺陷。
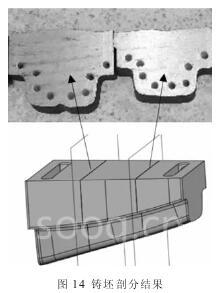
由于得到的鑄坯尺寸已經(jīng)接近所需要的模具尺寸, 所以鑄坯進行相關(guān)熱處理及一次表面精加工即可得到最后的熱沖壓模具。
5 、結(jié)論
汽車熱沖壓模具由于內(nèi)部存在隨形冷卻水道 , 生產(chǎn)制作難度很大 。 本文結(jié)合3D打印技術(shù) 、傳統(tǒng)砂型鑄造技術(shù)以及鑄造模擬技術(shù) 、三 維掃描技術(shù) , 提出汽車熱沖壓模具 的數(shù)字化鑄造技術(shù) 。 利用鑄造模擬技術(shù)設(shè)計優(yōu)化出最合適的鑄造方案 ,通過3D打印技術(shù)打印出高精度的砂型 ,將砂型組合后進行澆注得到高精度的鑄坯 ,在整個過程中 , 通過三維掃描技術(shù)對各個環(huán)節(jié)的產(chǎn)品進行精度評價 。 整個技術(shù)路線中 ,每個環(huán)節(jié)都可以通過數(shù)字化控制與調(diào)節(jié)以保證熱沖壓模具的成型質(zhì)量 。
此種工藝路線對于汽車熱沖壓模具這類內(nèi)部復(fù)雜結(jié)構(gòu)的鑄件成形具有示范意義。
(轉(zhuǎn)載)