0 引言
回彈是板料沖壓成形中普遍存在的問題,并最終影響零件的尺寸精度。解決沖壓零件回彈的方法主要有兩種:① 通過選擇合適的成形方案和工藝參數(shù)減少零件的回彈量;② 對(duì)模具型面給予一定反向回彈補(bǔ)償。在實(shí)際模具開發(fā)中。第一種方法主要用于減少零件成形后的回彈量,無法完傘消除回彈。因此可能最終零件的尺寸偏差仍超出零件的許用公差范圍。對(duì)模具型而進(jìn)行回彈補(bǔ)償成為零件尺寸精度控制的重要手段。該方法在實(shí)際中應(yīng)用得十分廣泛。
近年來,諸多學(xué)者針對(duì)回彈補(bǔ)償方法進(jìn)行了大量研究。王發(fā)成等采用Dynaform軟件對(duì)某葉片進(jìn)行沖壓成形模擬和回彈計(jì)算,并借助回彈補(bǔ)償模塊,采用有限元方法預(yù)測(cè)回彈量并進(jìn)行相應(yīng)的回彈補(bǔ)償。聶昕等采用型面整體變形算法對(duì)汽車梁類零件的型面進(jìn)行回彈補(bǔ)償,該方法能有效提高回彈補(bǔ)償效率,且具有高精度和補(bǔ)償準(zhǔn)確的特點(diǎn)。馮楊等提出了一種基于補(bǔ)償因子的模面修正方法,該方法將零件的型面分成多個(gè)截面,在各截面上實(shí)施不同的補(bǔ)償因子,以提高型面補(bǔ)償精度。Sheu等提出采用雙弧曲面模型(Bi-arc surface model)對(duì)扣描的沖壓件的點(diǎn)云數(shù)據(jù)進(jìn)行逆向建模.并以此對(duì)模具進(jìn)行同彈補(bǔ)償。
現(xiàn)有研究主要集中在形狀簡(jiǎn)單或者零件本身具有基準(zhǔn)平面和基準(zhǔn)孔的零件。然而,針對(duì)復(fù)雜曲面零件回彈補(bǔ)償?shù)难芯枯^少。本文以某大型核電汽輪機(jī)空心葉片外弧為例,提出采用三維掃描儀對(duì)沖壓成形的葉片零件進(jìn)行三維全型面檢測(cè),通過進(jìn)行逆向建模得到掃描模型,并與設(shè)計(jì)模型進(jìn)行對(duì)比得出實(shí)際回彈量,采用逆向數(shù)據(jù)進(jìn)行準(zhǔn)確的回彈補(bǔ)償。
1 三維全型面檢測(cè)方法
圖1為某大型核電汽輪機(jī)空心葉片外弧零件的三維圖。該零件的制造工藝為落料、熱沖壓成形、激光切割、焊接(與內(nèi)弧零件)和二次激光切割。圖1所示葉片外弧有11個(gè)平行的截面(C1~C11),實(shí)際生產(chǎn)中將零件放置在具有11個(gè)相同截面尺寸的專用槍具上。采用間隙尺測(cè)量實(shí)際零件與截面的偏差量。本文所研究葉片外弧零件的截面絕對(duì)偏差小于等于1.5mm。

圖1 空心葉片外弧零件
在對(duì)零件尺寸是否合格的評(píng)判方面,采用傳統(tǒng)檢具的截面檢測(cè)方法具有較高效率,但對(duì)于不合格的零件,需要對(duì)模具型面進(jìn)行回彈補(bǔ)償,采用傳統(tǒng)檢測(cè)方法進(jìn)行回彈補(bǔ)償十分麻煩。由于葉片的型面復(fù)雜,傳統(tǒng)的檢具檢測(cè)化置有限,且利用檢測(cè)數(shù)據(jù)進(jìn)行建模修改麻煩,導(dǎo)致對(duì)模具模面補(bǔ)償?shù)倪^程十分耗時(shí),且準(zhǔn)確度不高。針對(duì)類似的具有復(fù)雜曲面的零件,本文提出采用三維全型面掃描的方法來檢測(cè)零件,其檢測(cè)流程如圖2所示。
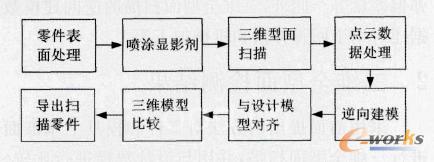
圖2 三維全型面掃描檢測(cè)方法
首先對(duì)零件進(jìn)行門描前的預(yù)處理(包括表面清理、噴涂顯影利和貼標(biāo)識(shí)點(diǎn))。考慮到該零件為復(fù)雜曲面,沒有任何特征面和特征孔,通常情況下對(duì)此類零件后續(xù)對(duì)齊常常采用手動(dòng)對(duì)齊和最佳擬合對(duì)齊,這些方法對(duì)齊誤差較大,對(duì)結(jié)果影響大。針對(duì)這類復(fù)雜曲面零件,本文提出將零件放置在模具上,在模具上選定基準(zhǔn),將零件和模具上的基準(zhǔn)的所有數(shù)據(jù)都進(jìn)行掃描和記錄,便于后續(xù)對(duì)齊比較,減少了對(duì)齊誤差。掃描檢測(cè)中選擇圖3(a)所示的3個(gè)基準(zhǔn)平面作為后續(xù)的對(duì)齊基準(zhǔn)平面。
圖3(b)為試驗(yàn)采用的三維全型面掃描設(shè)備,該設(shè)備為Shining 3D-Scanner系列三維掃描儀,型號(hào)為EaScan-D,產(chǎn)于中國浙江,其掃描精度為0.02 mm。該設(shè)備為非接觸式三維掃描方式,掃捕過程對(duì)被檢測(cè)物體沒有損傷,主要應(yīng)用于產(chǎn)品設(shè)計(jì)開發(fā)、逆向工程及工件檢測(cè)。本文借助該設(shè)備對(duì)復(fù)雜葉片外弧零件連同模具上的基準(zhǔn)一起進(jìn)行掃描,計(jì)算機(jī)可以獲得掃描后的點(diǎn)云數(shù)據(jù)。通過逆向建模軟件對(duì)得到的點(diǎn)云數(shù)據(jù)進(jìn)行處理(包括點(diǎn)云對(duì)齊、采集、降噪、封裝、填孔和修補(bǔ)等操作),得到掃描后的片體模型。最后,將模具上對(duì)齊的基準(zhǔn)平面和外弧零件的設(shè)計(jì)數(shù)模導(dǎo)人,用于與掃描模型的對(duì)齊和二維比較。通過三維比較可以得到三維掃描零件與實(shí)際設(shè)計(jì)模型的偏差量,該方法還可以用于分析零件孔位位置、孔位直徑、零件各邊回彈偏差量等。此外,三維全型面掃描的逆向建模數(shù)據(jù)還可用于 彈補(bǔ)償和機(jī)械加工等。
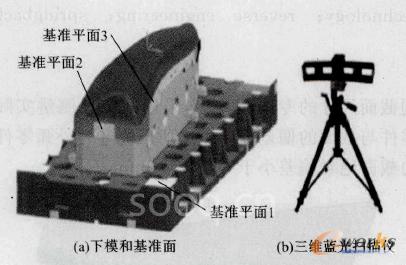
圖3 掃描基準(zhǔn)和使用掃描設(shè)備
2 三維全型面檢測(cè)結(jié)果
采用前面提出的方法對(duì)零件和模具上基準(zhǔn)面進(jìn)行三維全型面掃描,并用與沒計(jì)數(shù)模進(jìn)行比較。比較過程中基于模具上的3個(gè)基準(zhǔn)平面進(jìn)行對(duì)齊,3個(gè)平面對(duì)齊誤差分別為0、0.017和0.018mm。圖4為葉片外弧的三維比較偏差圖。由圖4可以得出:該零件的最大正偏差為2.59 mm;最大的尺寸負(fù)偏差為-3.04 mm。各個(gè)截面的二維截面偏差量可以通過截取截面查看,從左到右的l1個(gè)截面中,截面C2、C5、C6的最大絕對(duì)偏差值小于1.5 mm;其余截面部分區(qū)域超過了1.5mm。即零件尺寸偏差過大。圖4(b)為C8截面的二維尺寸偏差量。
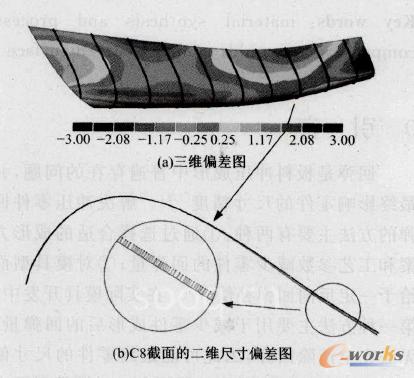
圖4 葉片外弧三維比較的偏差圖
通過掃描數(shù)據(jù)進(jìn)行逆向建模,一方面可以用于評(píng)價(jià)零件的三維和二維的偏差量;另一方面還可以用于模具型面的回彈補(bǔ)償。首先,導(dǎo)入三維掃描模型以及原始零件數(shù)模;然后,利用回彈補(bǔ)償算法反箅出回彈補(bǔ)償面;最后,利用所得到回彈補(bǔ)償數(shù)據(jù)加工模具。
3 基于逆向工程的回彈補(bǔ)償
圖5為本文采用的基于掃描數(shù)模的回彈補(bǔ)償示意圖。假設(shè)本文所研究的零件是由”個(gè)節(jié)點(diǎn)組成的有限元網(wǎng)格集合R3。圖5(a)中所示數(shù)模滿足以下關(guān)系:

節(jié)點(diǎn);n為零件節(jié)點(diǎn)總數(shù);a為補(bǔ)償因子,補(bǔ)償因子a通常為負(fù)值,其值為-2.5~-1.0,與材料的性能和厚度有關(guān)。
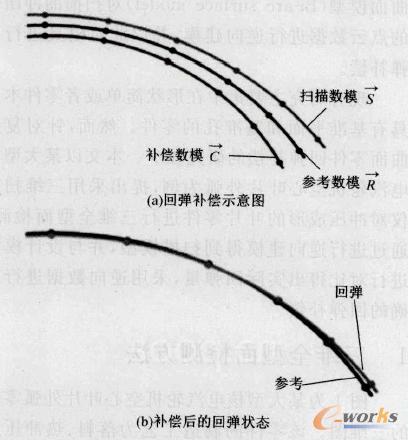
圖5 基于掃描數(shù)模的回彈補(bǔ)償示意圖

基于逆向工程的回彈補(bǔ)償流程如圖6所示?;貜椦a(bǔ)償原理是:首先,計(jì)算三維掃描模型與參考模型的節(jié)點(diǎn)偏差量;然后,根據(jù)圖5所示的回彈補(bǔ)償方法對(duì)零件進(jìn)行相應(yīng)的回彈補(bǔ)償.回彈補(bǔ)償借助華天軟件Sinovation計(jì)算實(shí)現(xiàn),補(bǔ)償系數(shù)設(shè)為-1.0,回彈補(bǔ)償結(jié)果如圖7所示。從圖7可以得出:左邊放大區(qū)域補(bǔ)償數(shù)模在最下層,參考數(shù)模在中間。掃描數(shù)模位于最上層;右邊局部放大區(qū)域,最上層為補(bǔ)償?shù)玫降钠w。中間為零件參考數(shù)模,最下層為實(shí)際三維掃描的零件模型。
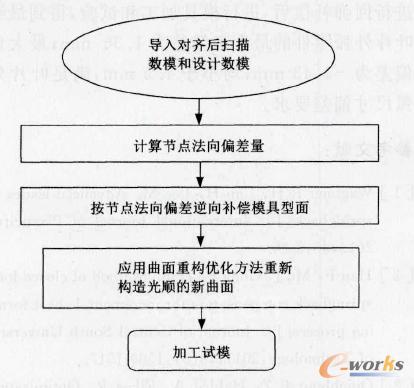
圖6 基于逆向工程的回彈補(bǔ)償流程圖
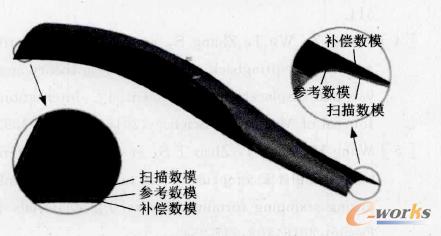
圖7 回彈補(bǔ)償結(jié)果
4 試驗(yàn)
采用逆向工程數(shù)據(jù)進(jìn)行問彈補(bǔ)償?shù)男兔婵捎糜谥苯蛹庸つ>?。試?yàn)中零件的掃描模型和對(duì)比參考數(shù)模均為零件的上層片體模型, 此補(bǔ)償數(shù)模用于直接加工模具的凹模型面,凸模和壓邊圈的模具型面需偏置一個(gè)料厚進(jìn)行編程加工。由于葉片外弧零件的拉延成形設(shè)備為常規(guī)薄板成形液壓機(jī),零件的成形由工人操作,因此對(duì)饃具的閉合高度沒有嚴(yán)格尺寸要求。 在回彈補(bǔ)償后,對(duì)模具進(jìn)行二次加工,加工編程過程中,以現(xiàn)有模具刑面狀態(tài)作為待加工的原始狀態(tài),以回彈補(bǔ)償型面作為目標(biāo)型面狀態(tài),借助UG軟件加工編程模塊,采用整體最小加工量進(jìn)行數(shù)控力加工編程。圖8(a)(b)(c)為試驗(yàn)中加工的葉片外弧熱成形模具。
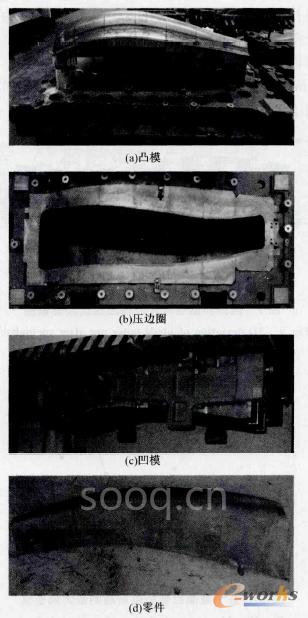
圖8 試驗(yàn)?zāi)>吆途€切割后的零件
試驗(yàn)步驟:① 將板料放人電阻爐中加熱到870℃,為保證板料內(nèi)外部加熱均勻且不發(fā)生過燒,達(dá)到?jīng)]定溫度870℃后再保溫6 min;② 試驗(yàn)中采用水基高分子和石墨乳作為潤滑劑,均勻地涂綴在模具型腔和壓料面上;③ 從加熱爐中取出板料并快速轉(zhuǎn)運(yùn)到模具上,整個(gè)轉(zhuǎn)運(yùn)時(shí)間控制在17~22 s內(nèi)。以保證板料不至于降溫太多;④ 壓機(jī)下行,對(duì)板料進(jìn)行熱沖壓成形;⑤ 凸凹模閉合后,保壓7.5 min;⑥壓機(jī)上行,取出成形后的葉片背弧零件;⑦ 將葉片放置在空曠位置,冷卻至室溫。
對(duì)得到的熱成形葉片外弧零件進(jìn)行激光切割,得到零件如圖8(d)所示。采用前面提出的三維全型面檢測(cè)方法對(duì)該零件進(jìn)行檢測(cè),利用Geomagic Qualify軟件對(duì)掃描模型以及設(shè)計(jì)模型進(jìn)行3D尺寸偏差比較,得到如圖9所示的回彈補(bǔ)償后葉片外弧三維比較偏差圖。圖10為各個(gè)截面凹彈補(bǔ)償前、后的最大偏差值。從圖10中可以看出:該葉片外弧的最大正偏差為1.36mm;最大的尺寸負(fù)偏差為-1.43 mm,其絕對(duì)值均小于1.5 mm,滿足葉片外弧尺寸偏差要求。
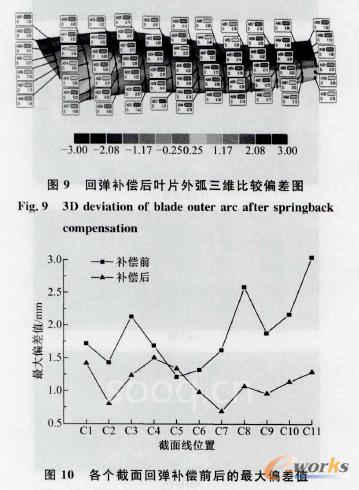
5 結(jié)論
(1)針對(duì)復(fù)雜曲面類零件提出了一種采用三維全型面掃描檢測(cè)零件,通過逆向建模得到掃描數(shù)模,并與設(shè)計(jì)模型進(jìn)行對(duì)比得出零件偏差量的方法。以葉片外弧零件為例,通過三維全型面檢測(cè)得出該零件的最大正偏差和負(fù)偏差分別為2.59mm和-3.04 mm。與傳統(tǒng)專用檢具相比。三維全型面檢測(cè)可以用于快速、全面地檢測(cè)各類復(fù)雜零件,具有檢測(cè)數(shù)據(jù)全和精度高的特點(diǎn)。
(2)針對(duì)常規(guī)復(fù)雜曲面零件偏差比較方法中對(duì)齊誤差大的問題,提出將零件放置在模具上,在模具上選定基準(zhǔn),將零件和模具上的基準(zhǔn)的所有數(shù)據(jù)都進(jìn)行掃描和記錄,便于后續(xù)對(duì)齊比較,減少對(duì)齊誤差。
(3)采用掃描數(shù)據(jù)進(jìn)行逆向建模,并用于對(duì)模具型面進(jìn)行回彈補(bǔ)償,提出基于逆向工程對(duì)復(fù)雜曲面零件進(jìn)行回彈補(bǔ)償?shù)姆椒ā?duì)葉片外弧零件進(jìn)行回彈補(bǔ)償后,進(jìn)行模具加工和試驗(yàn),得到最終葉片外弧零件的最大正偏差為1.36mm;最大負(fù)偏差為-1.43mm,均小于1.5mm,滿足葉片外弧尺寸偏差要求。
(轉(zhuǎn)載)